System flow mortar CERAfix 222
System flow mortar CERAfix 222
SYFLWMORT-(CERAFIX-222)-25KG
CERAFIX
Register now and access more than 125,000 products
- The almost self-levelling system flow mortar or thin screed can be laid universally indoors in layers of 10 to 40 mm thick as a level surface. It is therefore suitable for use as a component of thin-layer floor renovation systems.
- Furthermore, the thin screed can be used as heated screed on underfloor heating and in domestic bathrooms.
CERAfix 222 must be able to dry out unimpeded and must not be exposed to excessive or permanent moisture.
The screed must always be re-finished by sanding if there are soft, unstable areas or thin, hard shells that are slightly loose on the surface. WÜRTH CERAfix 222 is not liable to such surface finishing issues provided that it has been applied correctly (always observe the slump measurement). However, if such surface finishing issues occur, it is recommended that the screed be ground before it is covered. The division of the fields must be planned in accordance with information sheet 5 "Joints in calcium sulphate floating screed" of the VDPM/IWM. For floor coverings made of engineered wood, the required residual moisture as recommended by the floor covering manufacturer is decisive.
Caution: Depending on the machine performance, provide construction joints as necessary.
If CERAfix 222 is used for a thin-layer underfloor heating system, the specifications from WÜRTH must be observed.
Cement sulphate floating screed is not suitable for use in garages.
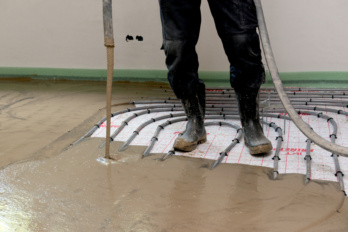
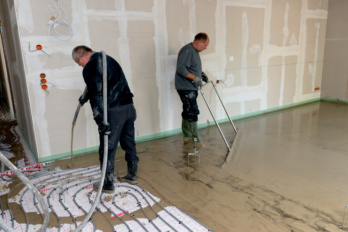
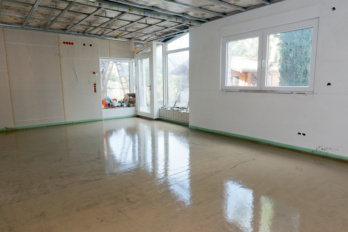
CERAfix 222 is suitable as a substrate for all common floor coverings (carpet, tiles, natural stone, parquet). The almost self-levelling thin coating can be used universally in indoor areas with layer thicknesses of 10 to 40 mm (taking into account DIN 18560) and is therefore suitable for use as part of thin-layer floor renovation systems. The thin coating can be used on top of underfloor heating, taking into account the necessary pipe partitions.
The indoor screed has been tested by the Fraunhofer Institute for Building Physics in accordance with AgBB scheme 2018 and is classified as particularly low-emission. Ideally, each room should be separated by a corresponding expansion joint due to the impact noise. For installation in wet rooms, the notes and guidelines for the planning and application of calcium sulphate floating screed apply. Please pay particular attention to the currently valid version of leaflet "Calcium sulphate floating screed in wet rooms" of VDPM e.V. and Bundesverband der Gipsindustrie e.V.
Application conditions:
- Ambient temperature and substrate temperature during application and drying: 5-30 °C
- Due to their instability when subjected to alkaline environments, bare aluminium profiles must not be used as a substrate.
- Protect from the elements (cold, frost, heat, direct sunlight, humidity, rain, wind, draughts etc.) until fully dry.
Application:
The correct consistency is set at the start of the work by determining the slump. For this purpose, a one-litre test can (filling height 26 cm, diameter 7 cm) is placed on a PE film and filled with material, lifted upwards and the slump measured.
Once the screed has been poured level, it must be tamped crosswise with a dapple bar or hard broom. This removes trapped air pockets and levels the screed material.
When used as heated screed, the material should be applied with the underfloor heating switched on at a max. flow temperature of 20 °C.
Chemical basis | Cement |
Colour | Grey |
Mixing ratio | 4,25 – 5 l for 25 kg |
Processing time | 30 min |
Application quantity per coating thickness | 1.9 kg/mm/m² |
Min./max. processing temperature | 5 to 30 °C |
Application conditions | at min. 5°C and max. 80% relative humidity |
Max. processing time | 60 min |
Hardening time | 2 h |
May be walked on after max. | 36 h |
May be walked on in following conditions | at 20°C and 65% relative humidity |
Full resilience | 7 d |
Conditions for full resilience | at 20°C and 65% relative humidity |
Min. processing temperature | 5 °C |
Max. processing temperature | 30 °C |
Min. compressive strength | 30 N/mm² |
Compressive strength conditions | after 28 days, 22°C and 65% relative humidity |
Min. flexural strength | 8 N/mm² |
Building material class | A1 - Non-flammable |
Weight of content | 25 kg |
Contents | 25 l |
Container | Paper bag |
Shelf life from production | 9 Month |
Conditions to maintain shelf life from production | cool storage area |
Grit | 0-2 mm |
Litre yield | Approx. 525 l /42 bags |
Coverage | Approx. 19 kg/m2/cm |
Can be heated | After 7 days |
Slump measurement | 380-420 mm |
Screed type | CA-CT C30-F8 |
Maturity for vapour-tight coverings | 1.3 % CM humidity (approx. 8 d with layer thickness of 25 mm, at 20°C and 65 % RH) |
Maturity for vapour-permeable coverings | 1.8 % CM humidity (approx. 6 d with layer thickness of 25 mm, at 20°C and 65 % RH) |
Datasheets (1)
Certificates/ Documents (0)