2C casting and adhesive resin CERAfix® 203
2C cast/adhesive resin, CERAfix 203
FILR-2K-HARZ-(CERAFIX-203)-5X0,5KG
CERAFIX

Register now and access more than 125,000 products
Three-chamber bag
- Very clean processing incl. glove and screed clips
- Portion bags to suit requirements make for easy, quick dispensing
- Easy to mix in the bag without the need for tools
Excellent creep and penetration properties
- Penetrates into the thinnest cracks
- Easy to use
Highly adhesive
- Creates force-locked and lasting connections
- Excellent adhesion to mineral surfaces
Fast curing
- Reduces downtimes
- Reworking can be performed quickly
Resistant to chemicals
Versatile applications, including areas subject to high stresses, such as craft trades and industry
Water- and frost-resistant once hardened
Suitable for floor heating and electric heating mats
- Take care, as the remaining material in the sausage pack can get hot!
- Cannot be used for structural areas
- Do not seal cracks and dummy joints until the surface is ready to be covered
- Do not seal cracks and dummy joints until the screed has matured (permitted CM moisture)
- Moisture and contamination can severely impair the adhesion of the individual layers to each other!
- Higher temperatures shorten the application and curing time. Lower temperatures increase the application and curing time. The material consumption also increases at lower temperatures.
- After long interruptions/waiting times between the individual coats, the surface must be cleaned well and thoroughly sanded. A completely new casting resin must then be applied.
- After application, the layer must be protected from moisture. Exposure to moisture too early will cause whitening and/or tackiness of the surface and may cause the curing process to fail. Tacky or discoloured surfaces must be removed and reapplied.
- Cured product residues can be disposed of in accordance with waste code EAK 17 02 03, plastic. Liquid product residues can be disposed of in accordance with waste code EAK 08 01 11, paint and paint waste containing organic solvents or other hazardous substances.
- To assess how mature the covering is, perform a moisture measurement using the CM device.
- Edge, field, building and movement joints must be observed. These must be retained or incorporated at the prescribed location and sealed off by suitable means, e.g. edge strips!
- The technical data sheets of the products used must be observed!
- Protect surfaces that do not require treatment against exposure to CERAfix 203!
- Currently applicable regulations must be observed!
For example:
- DIN 18157
- DIN 18352
- DIN 18560
- DIN EN 13813
- DIN 1055
- TKB information sheets from Industrieverband Klebstoffe e. V. (Industry Association of Adhesives)
- BEB information sheets, published by Bundesverband Estrich und Belag e. V. (Federal Association for Screeds and Coverings).
- Technical information "Interface coordination for heated floor structures".
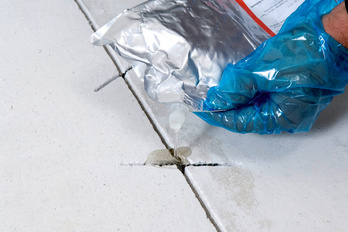
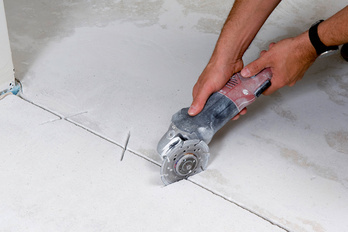
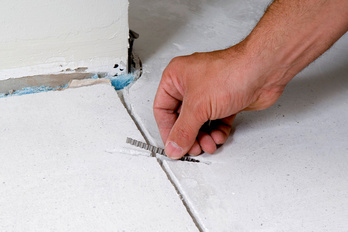
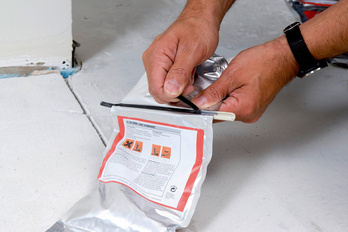
The usage instructions are recommendations based on the tests we have conducted and our experience; carry out your own tests before each application. Due to the large number of applications and storage and processing conditions, we do not assume any liability for a specific application result. Insofar as our free customer service provides technical information or acts as an advisory service, no responsibility is assumed by this service except where the advice or information given falls within the scope of our specified, contractually agreed service or the advisor was acting deliberately. We guarantee consistent quality of our products. We reserve the right to make technical changes and further develop products.
CERAfix 203 is primarily used for pouring compound screeds with cavities and for producing positive bondings of cracks and joints in screed and concrete.
It is also suitable for use as primer resin, for touching up and repairing stone and concrete chips etc. where small quantities of resin are required. We recommend using CERAfix 103 if working over a large area.
CERAfix 203 is suitable for hot screeds, for indoor and outdoor use and for environments exposed to moisture.
For use as a binder for epoxy resin mortars to seal openings and around installed parts.
The contents of the bag are mixed as follows for all applications:
Suitable protective equipment (safety goggles/face guards, gloves) must be used! The hardener is acidic! Open the third chamber without damaging the first and second chambers. Take out the disposable gloves and screed braces. Pull the round cord out of the securing strip so that the contents of the first and second bag chambers can be mixed together. Thoroughly mix the two matched components for approx. 3 minutes by kneading and churning them. The ready-to-use material is to be mixed evenly and so that there are no streaks. Ensure that the bag is not damaged during mixing. Put on the gloves. Then open the screw cap and, where necessary, push on a piece of the plastic hose. Then squeeze out the material and apply immediately.
1. Sealing cavities:
- Drill or expose the cavity. The air must be able to escape from the cavity, so a second ventilation drill hole must be drilled
- Then thoroughly clean and remove dust from the area
- Then pour the mixed casting resin into the cavity in portions. Subsequent casting may be required. Material requirement: 1.1 kg/l volume
2. Sealing cracks:
- Open the crack and cut perpendicular to the crack at a distance of 15 to 20 cm; use a cutting disc to cut a depth of 1/2 to 2/3 of the screed thickness. The transverse slots should be positioned so they are central to the crack and should be approx. 10 cm in length
- Then thoroughly clean and remove dust from the area. It is recommended that the area be carefully cleaned of dust using an industrial vacuum cleaner
- Then pour the mixed resin into the crack and cutting joints in portions until it is visibly saturated. To extend the run-out, a piece of the enclosed plastic hose can be pushed on
- Then insert the screed braces into the transverse slot and evenly spread the emerging resin on the surface
- After approx. 30-45 minutes, spread fresh quartz sand with a grit of 0.2-1.0 mm diameter on top of the resin
- Once cured, mop and vacuum the loose sand
3. Priming:
- Prepare and clean the substrate according to the surface specifications
- Pour the mixed resin onto the substrate and spread evenly until saturation is visible
- After approx. 30-45 minutes, spread fresh quartz sand with a grit of 0.2-1.0 mm diameter on top of the resin
- Once cured, mop and vacuum the loose sand
4. Repairing chips:
- Prepare and clean the substrate according to the surface specifications.
- Then prime the area accordingly.
- A mortar is produced as follows to repair chips: For repairing greater crack depths, a mortar is made from CERAfix 203 bonding agent as follows: First add the quartz sand to the mixing bucket; then add the mixed resin. 1 mass part CERAfix 203: 7-10 mass parts quartz sand. Then mix together evenly. The quartz sand grit is matched to the coat thickness to be applied. The minimum coat thickness equates to approx. three times the largest grain size. The maximum coat thickness equates to approx. ten times the largest grain size. For example: The quartz sand used has a grit of 0-2 mm diameter. As a result, a mortar can be produced that can be applied in coat thicknesses of approx. 6-20 mm.
- Apply, compress and smooth the mixed mortar onto the freshly primed surface. Then immediately spread quartz sand with a grit of 0.2-1.0 mm diameter over the freshly laid mortar. Required: approx. 2.0 kg mortar per 1 m² and 1 mm coat thickness.
5. Scratch fillers:
- Prepare and clean the substrate according to the surface specifications
- Then prime the area accordingly
- Produce the mortar for filling scratches as follows: First add the quartz sand with a grit of 0.2-1.0 mm diameter to the mixing bucket; then add the mixed resin. 1 mass part CERAfix 203: 1-2 mass parts quartz sand. Then mix evenly
- Apply the mixed filler in a single pass using the scratch filling technology. Required: approx. 1.6 kg mortar per 1 m² and 1 mm coat thickness
- Then immediately spread fine quartz sand with a grit of 0.2-1.0 mm diameter over the freshly laid filler.
Surface:
The base material must be solid, load-bearing, clean, dry and free from separating substances. Separating materials or layers, such as layers of sinter, dust, oil, paints etc., must be removed with suitable measures such as blasting, milling, sanding, suction and/or degreasing. The substrate must have sufficient load-bearing capacity for the active loads - refer to DIN 1055. With screeds on separating or insulating layers, you need to check how mature the covering is before applying CERAfix 201. Concrete must comply with a minimum compressive strength of C20/25 in accordance with DIN 1045. Screed must meet class C25-F4 in accordance with DIN EN 13813 as a minimum and must have been in place for 28 days. The moisture content in line with the CM method must be less than 4 CM% for cement-based surfaces. For calcium sulphate screeds without underfloor heating, the CM moisture content must not exceed 0.5 CM%. For calcium sulphate screeds with underfloor heating, it must not exceed 0.3 CM%. Observe the prescribed residual moistures for subsequent coverings. When doing so, ensure that the permitted residual moisture content is observed in accordance with current technical leaflets. The CM measurement must be conducted in accordance with the current work instruction "Interface coordination for heated floor constructions". Subsequent moisture ingress must be prevented. During application and in the week after, the air, material and substrate temperature must be at least +8°C.
Weight of content | 2.5 kg |
Chemical basis | Two-component epoxy resin |
Density | 1.1 g/cm³ |
Min./max. processing temperature | 10 to 35 °C |
Colour | Transparent |
Full resilience | 7 d |
Container | 3-chamber bag |
Shelf life from production | 18 Month |
Conditions to maintain shelf life from production | cool and dry storage area, 10°C to 25°C |
Application conditions | at 20°C and 65% relative humidity |
May be walked on after max. | 6 h |
May be walked on in following conditions | at 20°C and 65% relative humidity |
Can be covered after max. | 6 h |
Conditions for full resilience | at 20°C and 65% relative humidity |
Resistance against | Chemicals, Frost (after hardening), Water (after hardening) |
Permissible moisture content of levelling mass and cement-based base material is determined using the CM device | |||
Flooring | Heated | Unheated | |
Ceramic tiles or natural/artificial stone | Medium-bed | 2.0 % | 2.0 % |
Thin bed | 2.0 % | 2.0 % | |
Water vapour diffusion-tight linings | 1.8 % | 2.0 % | |
Textile coverings | Blocks water vapour | 1.8 % | 2.5 % |
Permeable to water vapour | 2.0 % | 3.0 % | |
Parquet and laminate flooring | Floating installation | 1.8 % | 2.0 % |
The CM measurement must be conducted in accordance with the current work instruction FBH-AD from technical information "Interface coordination for heated floor constructions". |
Select RAL-colour code
!! NOTE: On-screen visualisation of the colour differs from real colour shade!!